Quality System Assurance

1. Quality Assurance:
1. Organization and staffing:
The company's quality control system and leading group are sound, with independent product quality management institutions: quality control center, full-time quality inspectors: 8 people. The company's production of product quality control are in accordance with GB/T19001/2015 preparation of the "quality manual" to implement the whole process of control. These include document control, record control, product realization planning control, process control with customer-related departments, procurement control, process monitoring and measurement control, product monitoring and measurement control, non-conforming product control and other control procedures. Attached are the quality management system structure chart, quality function distribution table, quality responsibilities and authorities of various personnel, and special inspection and test procedures.
2. Staff qualification and training:
Full-time quality inspectors have relevant professional skills and qualifications, have training plans, good training content and good training results.
3, to obtain third-party quality certification:
Obtaining ISO9001:2015 quality management, ISO14001:2015 environmental management and ISO45001:2018 occupational health and safety management third-party system certification.
4. Management of drawings, specifications and quality documents:
There is a special drawing data archive room and full-time administrator. The distribution and recovery of drawing data are controlled. The update degree of quality documents shall be strictly implemented according to the ISO9001:2015 quality management system documents.
2. quality inspection:
1, raw materials purchase control:
With a complete and standardized management of raw materials, purchased parts and incoming inspection system, external inspection, self-inspection documents and samples are kept intact and traceable, and the system can be well implemented.
2. Factory inspection capability:
The comprehensive performance test platform is advanced, the test site management system, operating procedures, and test standards are complete and complete, and various rules and regulations can be well implemented. On-site spot check 6 copies of factory inspection report, the test items are complete and standard, on-site random samples for factory test, the main test items include: physical and chemical indicators and mechanical properties, the test results are qualified.
3. Measurement and management of testing equipment:
The test data shall be recorded in a complete and standardized manner, with test personnel who can skillfully operate the equipment, master the test methods, be familiar with the product standards, and be able to skillfully and accurately judge the test results.
4. Control and prevention of nonconforming products:
Dispose of nonconforming products according to ISO9001:2015 quality management system documents, and spot check has records of nonconforming products.
5. Customer Complaint System:
There is a customer complaint handling management system, functional departments and personnel, complaint records and handling, correction and prevention, closing and project tackling results are clearly recorded.
3. system operation:
1, the company's three-standard integrated management system document on May 30, 2020 (version C) release and implementation, the chemical pump (process pump, slurry pump, vortex pump, axial flow pump, mixed flow pump) and the manufacturing and service of the mixer involved in the five departments and senior management for QES management.
2. Since its operation, the company's leaders, departments and all management personnel have attached great importance to the operation of the integrated management system, carried out publicity and education activities in various forms, publicized the company's quality, environment and occupational health and safety policies and objectives, and trained the management principles, basic principles, operation mode, management system documents and requirements of the integrated management system for managers and technicians.
3. In accordance with the provisions of the integrated management system document, each department and each position further clarify their respective management responsibilities, adjust, enrich and improve the responsibility system and management objectives of functional departments and positions at all levels, and on the basis of the original technology, quality assurance, safety standardization, civilized production and cost and capital management, the new requirements of the integrated management system will be added, gradually integrated into the product project tender preparation, production planning, resource allocation, supervision and management activities. Personnel at all levels pay attention to the requirements of customers, employees and society, meet the requirements of laws and regulations, and continuously improve the quality, occupational health and safety and environmental management performance. The integrated management system is being established and implemented in accordance with the system documents. The physical quality of products, hazards and environmental factors at the production site and related sites are all under control, and the continuous improvement mechanism is gradually improved and improved.
4. System audit statistics: quality objective: contract performance rate 100; The qualified rate of one-time inspection of products is 97% ~ 99%. The customer complaint disposal rate is 100. The quality accident is 0; Customer satisfaction rate is 97.8; Environmental objectives and indicators: wastewater discharge standard; Waste gas discharge standard; Noise emission standard; Solid waste shall be treated according to regulations. Put an end to environmental pollution incidents; The timely rate of environmental complaint handling is 100. Occupational health and safety objectives and indicators: fire accident is 0; minor injury accident rate is 0; serious injury and death accident rate is 0; occupational disease rate is 0; food poisoning event rate is 0; occupational hazard post staff physical examination rate is 100%. All environmental factor indicators are controlled within the standard range, no major environmental hazard accidents, no major fire accidents and acute poisoning accidents have occurred, and illegal command, illegal operation, and violation of labor discipline are eliminated.
In general: the responsible persons of each department are clear about their quality, environment and occupational health and safety functions and perform well; the planning process, monitoring and measurement process and after-sales service process of chemical pumps (process pumps, slurry pumps, vortex pumps, axial flow pumps, mixed flow pumps) and mixer manufacturing and service products can operate normally and are effectively controlled, it ensures that the quality of various pumps and mixers provided by the company to customers meets the requirements of customers and meets the requirements of relevant laws and regulations. The company's quality, environment and occupational health and safety policies and objectives can be effectively implemented and implemented in the company, and the integrated management system meets the requirements of quality, environment and occupational health and safety standards and management system documents. In the process, there are also some problems to be further improved and improved in the establishment and implementation of the three systems. The reasons are:(1) the staff's awareness of quality, environmental protection and safety is still relatively weak and needs to be further improved;(2) The requirements of system standards/documents are not well understood, not deeply understood and applied, and not mastered the operation skills;(3) The combination between the requirements of the three-standard system and the daily management of various departments is not well done, there is a disconnection, and the implementation of dynamic management is not thorough. Therefore, all departments should pay more attention to the operation of QES system. The controlled state of the production process and the stability of the product quality should be strengthened. In actual operation, effective improvement measures should be implemented (such as delimiting the company's safety marking in combination with the requirements of three-level safety standardization; Implement environmental standardization management and improve the company's on-site environment, etc.) to improve the effectiveness of system operation.
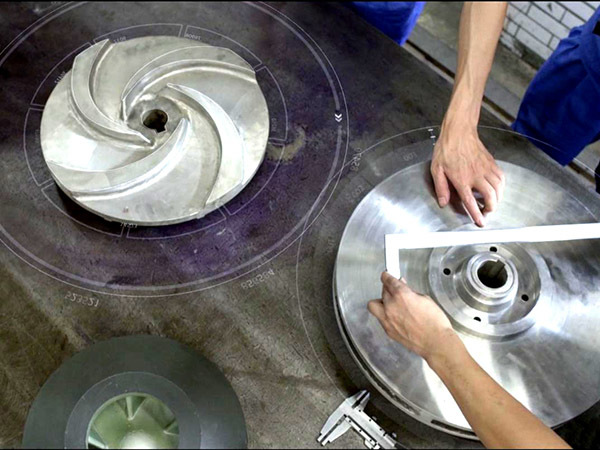
Company quality inspection
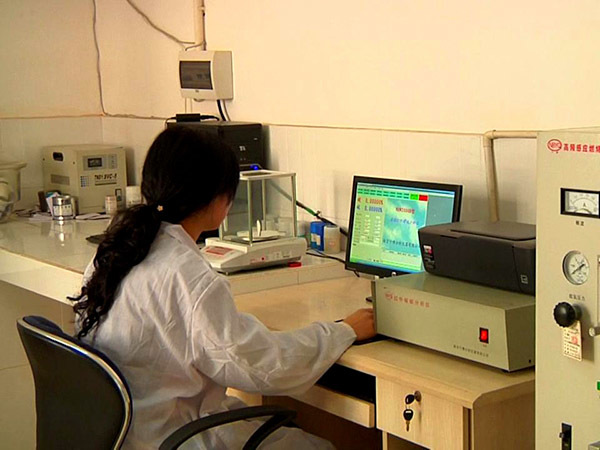
Company quality inspection
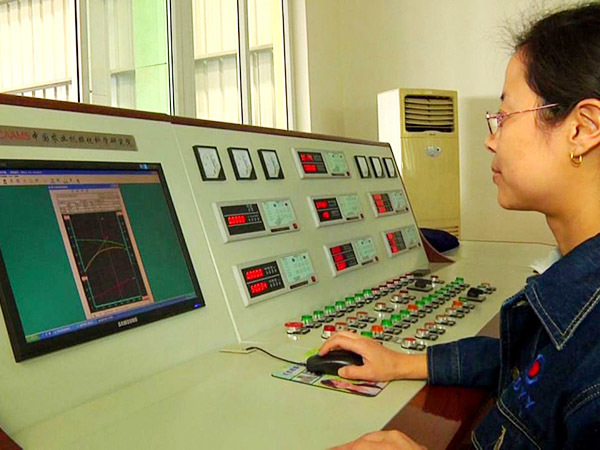
Company quality inspection
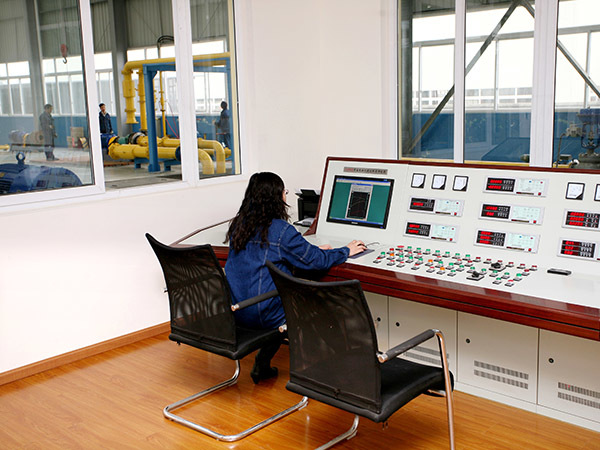
Company quality inspection